News Center
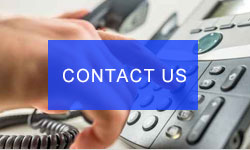




Where you are:Home>>New Center>>Company News
Attention to the safety of foundry production
The key of metal casting process design is the determination of the casting position, the design of the pouring system and the control and adjustment of the working temperature of the mould. Pouring position of casting 1. It is directly related to the metallic mold core and surface quantity, liquid metal into position, exhaust patency and metal structure complexity, to determine the distribution of metal processing and operation difficulty degree and cooling of casting temperature, thereby affecting the production efficiency of the casting, dimensional accuracy and quality. Therefore, casting location is an important part of the casting process design. 2) pouring system. The design of casting pouring system determines the quality of the inner and outer parts of the casting. The pouring system should have the function of skim, exhaust and feeding, and the reasonable solidification and cooling temperature field should be guaranteed. The correct and reasonable gating system except by empirical estimation, numerical simulation of casting solidification process can directly predict the temperature field numerical display, the casting shrinkage porosity (hole) of the dangerous position, so as to guide the design process, and their system structure and size, through the adjustment of cast metal structure, controlling the cooling rate or adjust the thickness of coating layer and other means to adjust the temperature and eliminate the casting defects, such as the blank bottom gating of the automobile engine aluminum cylinder head, despite the temperature field set almost more than the weight of the casting riser in the upper and bottom water is forced through technological measures is difficult to adjust the order of solidification reasonable, it is difficult to eliminate the bottom the inner gate around overheating and causing shrinkage defects. The introduction of a factory in France Sifa aluminum alloy casting machine is the use of such pouring system, the production process is not stable. 100 percent of the cylinder head to be infiltration, for shrinking cylinder head loose serious even infiltration also failed to meet the requirement of the withstand voltage; and from the riser injected directly into the molten steel, molten steel through the ceramic filter purification backward person cavity, ensure the reasonable casting cooling gradient, namely bottom-up order solidification mode, eliminating the shrinkage defects and head as well as the finished product rate increased significantly. British Foseco company has done a detailed study of the two kinds of casting methods and comparative test of the work piece, and called the latter DYPUR method. The method makes the model simple and compact, saves the aluminum liquid, and has high finished product rate. Using this method, even if a small amount of inclusion defects caused by the high drop of the aluminum liquid, the mechanical properties and air tightness of the castings are not affected. Of course, the opening position, structure and size of the pouring system in addition to the casting solidification temperature, but also need to take into account the degree of complexity, metal liquid filling is stable, whether with skim and exhaust and other functions. 3) metal working temperature. Similarly, the temperature of the metal working temperature and the temperature of each part of the cooling temperature field of the casting has an important role. Forced water cooling and air cooling in the local area of the metal is to ensure the normal working temperature, increase the production efficiency, and eliminate the heat, ensure the normal cooling temperature field. The more advanced and effective means of controlling the temperature of the cooling water is to control the outlet temperature of the cooling water, and the temperature of the outlet can be adjusted. Such as the Italy Fata company and the French Sifa company design and manufacture of metal type have advanced water, wind cooling device. In addition, for local heavy hot spot can be inlaid with thermal conductivity rate high or storage of metal inserts or adjusting thickness of coating layer and coating type to ensure reasonable temperature gradient in cooling of casting formation, partial shrinkage porosity (hole) defect elimination. Huizhou 0752-3522892 precision casting
Last one:More enquiries, fewer orders
Next article:About company