News Center
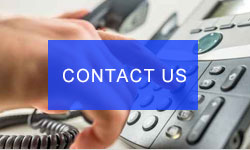




Where you are:Home>>New Center>>Company News
precision casting
Definition of scientific and technological terms
Chinese name:
precision casting
English name:
Casting precision
definition:
Casting method for precision casting by precision casting mould.
Applied discipline:
Mechanical Engineering (first class); casting (two grade); special casting (three stage)
medical aircraft
Precision casting is a general term to obtain the precise casting technology with the precise modeling method.
Basic concepts of precision casting
It includes: investment casting, ceramic mold casting, metal casting, pressure casting, lost foam casting.
Which is more commonly used is melt mold casting, also known as the lost wax casting: selection of suitable casting mould materials of (such as molten mould made of Paraffin); in the casting was repeated dip refractory coating and cast refractory sand process, hardening type shell and dry; the internal revestment melt away and get cavity; shell firing to obtain sufficient strength and burn the residual melt mold materials,; pouring need metal materials; solidification shell after sand cleaning to obtain high accuracy of the finished product. According to the needs of the product or the heat treatment and cold processing and surface treatment.
Development of precision casting
Precision casting, also known as lost wax casting, its product precision, complex, close to the final shape of the parts, can not be processed or rarely used directly, so investment casting is a near net shape of the advanced technology.
In ancient China, Wu Ding: Prince copper ban, bronze and so on, are casting a masterpiece. Since the 1940s investment casting for industrial production, half a century has been developing at a faster pace. Especially the rapid development of European and American countries. Now the investment casting used in aviation, weapons department outside, almost in all industrial sectors, particularly in electronics, petroleum, chemical industry, energy, transportation, light industry, textile, pharmaceutical, medical device, pump and valve etc. departments. In recent years, our country has developed rapidly.
Investment casting technology to the development of the melt mold casting can not only production of small-sized castings, but also in the production of large castings, the biggest investment castings contour size and nearly 2m, and the minimum wall thickness is less than 2mm. At the same time investment casting became more and more sophisticated, except for linear tolerance, components can also be reached higher geometric tolerances. Castings surface casting angle value is also getting smaller and smaller, reach Ra0.4 m.
Ceramic casting
Casting method for casting mould made of ceramic paste. Ceramic slurry by the hydrolysates of ethyl silicate and texture than the pure and thermal stability of high fine refractory sand such as hybrid electric melting quartz, zircon and corundum. In order to make ceramic slurry in a short period of time glue, often adding calcium hydroxide as a catalyst or Magnesium Oxide. Due to the use of the refractories ingredients and appearance are similar with ceramic, is called ceramic type. Ceramic mold casting is a new technology developed on the basis of ordinary sand casting. There are two types of ceramic types: 1. The ceramic type is made of ceramic slurry. The production process is the first shape is fixed on the plate, coat sand box, and then transfer a good ceramic slurry into the sand box, to be the plastic hardening the newcomer mode, calcined at high temperature to become namely casting. The use of bushing, the gap between the lining and the shape of the casting of ceramic slurry casting. Liner can be used sand, also can use metal type. The ceramic shell layer can be used to save a lot of ceramic slurry, and it can be used widely in the production. The surface roughness of ceramic castings can reach Ra10 ~ 1.25 microns, and the size precision is up to 3 ~ 5, which can achieve the purpose of cutting machining. Ceramic mold casting production cycle is short, high utilization rate of metal. The biggest can reach more than ten tons of castings, mainly used for casting large wall thickness precision castings and casting a single piece and small batch dies, forging dies, plastic mold, metal mold, die-casting mold, glass mold and other mold. The service life of the ceramic mold casting mold can be comparable with that of the mould made of mechanical processing method, and the manufacturing cost is lower than that of the mould made by mechanical processing method.
Brief introduction of sand casting
Give priority to the use of sand casting according to statistics
In all casting production in 60 ~ 70% by sand casting is produced, of which about 70% is used in the production of clay sand. The main reason is that the cost of sand casting is low compared with other casting method, simple production process, short production cycle. So as the automobile engine cylinder body, cylinder head, crankshaft castings are used clay wet sand production process. When the wet type can not meet the requirement to consider the use of clay sand table dry sand, dry sand mold or other. Wet clay sand casting casting weight can be from a few kilograms until tens of kilograms, but the clay does production of castings can be weighed dozens of tons.
Generally speaking, for medium and large castings, cast iron can be used resin self hardening sand, steel castings can be water glass sand to produce, can obtain the precise size, smooth surface castings, but the cost is relatively high.
Of course, sand casting production of precision casting, surface roughness, material density and microstructure and mechanical properties is often poor, so when the properties of casting requirements higher and other casting methods should be adopted, such as melt mold (lost wax casting, die-casting, low pressure casting and so on.
The casting method should adapt to the production batch.
For example, sand casting, a large number of production factories should create conditions using advanced technology design, core making method. Old shock or jolt squeeze moulding machine production line productivity is not high enough, high labor intensity of workers, large noise, does not meet the requirement of mass production should be gradually change. For small castings, the production line of horizontal and vertical type high pressure molding machine can be used.
Chinese name:
precision casting
English name:
Casting precision
definition:
Casting method for precision casting by precision casting mould.
Applied discipline:
Mechanical Engineering (first class); casting (two grade); special casting (three stage)
medical aircraft
Precision casting is a general term to obtain the precise casting technology with the precise modeling method.
Basic concepts of precision casting
It includes: investment casting, ceramic mold casting, metal casting, pressure casting, lost foam casting.
Which is more commonly used is melt mold casting, also known as the lost wax casting: selection of suitable casting mould materials of (such as molten mould made of Paraffin); in the casting was repeated dip refractory coating and cast refractory sand process, hardening type shell and dry; the internal revestment melt away and get cavity; shell firing to obtain sufficient strength and burn the residual melt mold materials,; pouring need metal materials; solidification shell after sand cleaning to obtain high accuracy of the finished product. According to the needs of the product or the heat treatment and cold processing and surface treatment.
Development of precision casting
Precision casting, also known as lost wax casting, its product precision, complex, close to the final shape of the parts, can not be processed or rarely used directly, so investment casting is a near net shape of the advanced technology.
In ancient China, Wu Ding: Prince copper ban, bronze and so on, are casting a masterpiece. Since the 1940s investment casting for industrial production, half a century has been developing at a faster pace. Especially the rapid development of European and American countries. Now the investment casting used in aviation, weapons department outside, almost in all industrial sectors, particularly in electronics, petroleum, chemical industry, energy, transportation, light industry, textile, pharmaceutical, medical device, pump and valve etc. departments. In recent years, our country has developed rapidly.
Investment casting technology to the development of the melt mold casting can not only production of small-sized castings, but also in the production of large castings, the biggest investment castings contour size and nearly 2m, and the minimum wall thickness is less than 2mm. At the same time investment casting became more and more sophisticated, except for linear tolerance, components can also be reached higher geometric tolerances. Castings surface casting angle value is also getting smaller and smaller, reach Ra0.4 m.
Ceramic casting
Casting method for casting mould made of ceramic paste. Ceramic slurry by the hydrolysates of ethyl silicate and texture than the pure and thermal stability of high fine refractory sand such as hybrid electric melting quartz, zircon and corundum. In order to make ceramic slurry in a short period of time glue, often adding calcium hydroxide as a catalyst or Magnesium Oxide. Due to the use of the refractories ingredients and appearance are similar with ceramic, is called ceramic type. Ceramic mold casting is a new technology developed on the basis of ordinary sand casting. There are two types of ceramic types: 1. The ceramic type is made of ceramic slurry. The production process is the first shape is fixed on the plate, coat sand box, and then transfer a good ceramic slurry into the sand box, to be the plastic hardening the newcomer mode, calcined at high temperature to become namely casting. The use of bushing, the gap between the lining and the shape of the casting of ceramic slurry casting. Liner can be used sand, also can use metal type. The ceramic shell layer can be used to save a lot of ceramic slurry, and it can be used widely in the production. The surface roughness of ceramic castings can reach Ra10 ~ 1.25 microns, and the size precision is up to 3 ~ 5, which can achieve the purpose of cutting machining. Ceramic mold casting production cycle is short, high utilization rate of metal. The biggest can reach more than ten tons of castings, mainly used for casting large wall thickness precision castings and casting a single piece and small batch dies, forging dies, plastic mold, metal mold, die-casting mold, glass mold and other mold. The service life of the ceramic mold casting mold can be comparable with that of the mould made of mechanical processing method, and the manufacturing cost is lower than that of the mould made by mechanical processing method.
Brief introduction of sand casting
Give priority to the use of sand casting according to statistics
In all casting production in 60 ~ 70% by sand casting is produced, of which about 70% is used in the production of clay sand. The main reason is that the cost of sand casting is low compared with other casting method, simple production process, short production cycle. So as the automobile engine cylinder body, cylinder head, crankshaft castings are used clay wet sand production process. When the wet type can not meet the requirement to consider the use of clay sand table dry sand, dry sand mold or other. Wet clay sand casting casting weight can be from a few kilograms until tens of kilograms, but the clay does production of castings can be weighed dozens of tons.
Generally speaking, for medium and large castings, cast iron can be used resin self hardening sand, steel castings can be water glass sand to produce, can obtain the precise size, smooth surface castings, but the cost is relatively high.
Of course, sand casting production of precision casting, surface roughness, material density and microstructure and mechanical properties is often poor, so when the properties of casting requirements higher and other casting methods should be adopted, such as melt mold (lost wax casting, die-casting, low pressure casting and so on.
The casting method should adapt to the production batch.
For example, sand casting, a large number of production factories should create conditions using advanced technology design, core making method. Old shock or jolt squeeze moulding machine production line productivity is not high enough, high labor intensity of workers, large noise, does not meet the requirement of mass production should be gradually change. For small castings, the production line of horizontal and vertical type high pressure molding machine can be used.
Last one:Company address change notice
Next article:More enquiries, fewer orders